鈦合金比重小(約4.5)、熔點高(1600℃左右)、塑性好,具有比強度高、耐蝕性強,能在高溫下長期工作(目前熱強鈦合金已用于500℃)等優點,因而已經越來越多地用作飛機和飛機發動機的重要承載部件,除了鈦合金材料的鍛件外,還有鑄件、板材(如飛機蒙皮)、緊固件等等。現代國外飛機上采用鈦合金的重量比已經達到30%左右,可見鈦合金在航空工業上的應用有著廣闊的前途。當然,鈦合金也存在如下缺點:例如變形抗力大、導熱性差、缺口敏感性較大(1.5左右)、顯微組織的變化對機械性能影響較顯著等,從而導致在冶煉、鍛造加工和熱處理時的復雜性。因此,采用無損檢測技術以保證鈦合金制品的冶金和加工質量,就是一個很重要的環節。
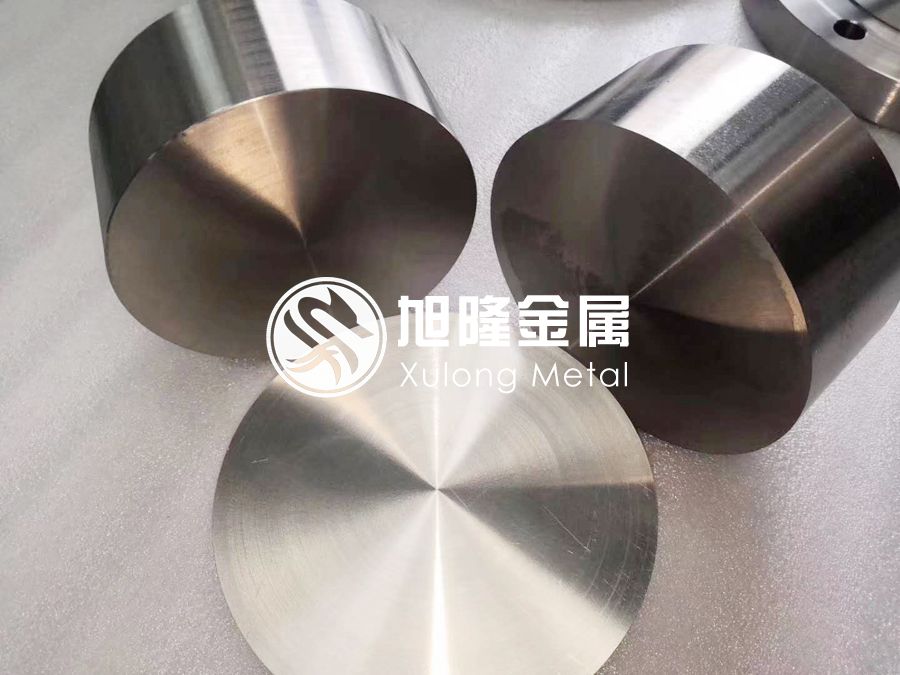
旭隆金屬結合鈦棒、鈦環、鈦管、鈦鍛件等產品的生產加工經驗,結合相關資料,將鈦合金鍛件中容易出現的缺陷,整理如下:
1、偏析型缺陷
除了β偏析、β斑、富鈦偏析及條狀α偏析外,最危險的是間隙型α穩定偏析(I型α偏析),其周圍常伴有細小的孔洞、裂紋,含有氧、氮等氣體,脆性較大。還有富鋁型α穩定偏析(II型α偏析),也因伴有裂紋并有脆性而構成危險性缺陷。
2、夾雜物
多是高熔點、高密度的金屬夾雜物。由鈦合金成分中高熔點、高密度元素未充分熔化留在基體中形成(例如鉬夾雜),也有混在冶煉原材料(特別是回收材料)中的硬質合金刀具崩屑或不適當的電極焊接工藝(鈦合金的冶煉一般采用真空自耗電極重熔法),例如鎢極電弧焊,留下的高密度夾雜物,如鎢夾雜,此外還有鈦化物夾雜等。
夾雜物的存在容易導致裂紋的發生與擴展,因此是不允許存在的缺陷(例如蘇聯1977年的資料中規定,鈦合金X射線照相檢查時發現直徑0.3~0.5mm的高密度夾雜物就必須予以記錄)。
3、殘余縮孔
1)Φ70mm鈦合金鍛棒中的殘余縮孔
縱波(上為縱波波形照片)與橫波(下為橫波波形照片)均能發現,縱波探測時表現為強烈的缺陷回波并造成底波降低(面積型缺陷,可大致判斷為徑向走向),橫波探測時表現為清晰強烈的缺陷回波(裂紋狀缺陷)。右圖為橫向低倍照片(1x)。
2)鈦合金餅坯中的鉬夾雜(高密度夾雜物)
這是冶煉時作為鋁鉬中間合金中的鉬未完全熔解而留在基體內形成,可用縱波探測到,無論改變超聲頻率及超聲波束直徑都能很好地發現,并且在兩面探測時位置對應良好。解剖后驗證為鉬夾雜。在橫向低倍上多呈“眼睛”狀,在餅坯中的取向多與端面平行,但也有的會取向傾斜,在餅坯上不易發現,待模鍛成盤形件后因變形力使其取向改變到與端面平行時才易于發現。左圖為橫向低倍照片(2x),右圖為按超聲束投射方向拍攝的X射線照片(外圈為鉛絲,中間的白點即為高密度夾雜物-鉬夾雜)
3)鈦合金餅(環)坯中的45°裂紋及鍛制板狀件上的十字裂紋
這類裂紋是由鍛造引起的,特別是從鈦錠開坯鍛制餅(環)坯時,往往因終端溫度過低、錘擊力過大等而沿最大變形應力方向開裂。這種裂紋大多在開口處彌合較緊,或者整條裂紋上的開隙度很不均勻,局部彌合很緊,經鍛造后機械加工至半成品時,如果表面恰好在彌合較緊的部位處,則用腐蝕或滲透法有時未必能發現,但其內部開裂又較大,甚至出現孔洞(如照片b))。采用45°折射橫波是很容易探測到并可以判斷的。
4)Φ70mm鈦合金軋棒上的徑向表面裂紋
這類裂紋也屬于鍛造或軋制加工中形成的裂紋,可以用腐蝕或滲透法發現,采用45°折射橫波作周面弦向掃查是很容易探測到的,而用一般的縱波周面徑向入射探測是發現不了的。
5)Φ125mm鈦合金鍛棒的中心粗晶:用5P14直探頭周面徑向探測,中心部位的雜波水平(同聲程比較)達到Φ1.2mm-6dB。
4、孔洞
孔洞不一定單個存在,也可能呈多個密集存在,會使低周疲勞裂紋擴展速度加快,造成提前疲勞破壞。
5、裂紋
主要指鍛造裂紋。鈦合金的粘性大,流動性差,加上導熱性不好,因而在鍛造變形過程中,由于表面摩擦力大,內部變形不均勻性明顯以及內外溫差大等,容易在鍛件內部產生剪切帶(應變線),嚴重時即導致開裂,其取向一般沿最大變形應力方向。
6、過熱
鈦合金的導熱性較差,在熱加工過程中除了加熱不當造成鍛件或原材料過熱外,在鍛造過程中還容易因為變形時的熱效應造成過熱,引起顯微組織變化,產生過熱魏氏組織。
相關鏈接